转自:蚌埠新闻网
树立行业标杆,讲好中国故事,传递中国声音,充分展现腾飞的中国经济、崛起的民族品牌和向上的企业家精神。近日,“崛起的民族品牌”专题系列节目对话天津世亚模具股份有限公司(简称:天津世亚)的董事长林世大先生,探讨模具领域的创新发展之路。
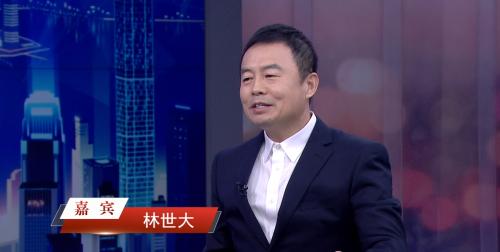
在汽车工业高速发展的今天,每一辆行驶在道路上的汽车都承载着无数技术创新与工艺突破。作为汽车安全结构的核心保障,模具的精度与可靠性直接关系到驾乘者的生命安全。天津世亚模具股份有限公司以匠心精神突破技术壁垒,用创新模具护航出行之路。
破局:以核心技术重塑行业格局
“模具是汽车安全结构件的灵魂。”林世大在访谈中开门见山地指出。在汽车制造领域,前后保险杠、车门槛、车门框等安全件的生产,都离不开高精度模具的支撑。传统模具在面对抗拉强度1180MPa的超高强度钢板时,往往面临回弹、开裂等技术瓶颈,而天津世亚通过自主研发的冷冲压成形技术,成功实现了这类材料的精密加工。
这项技术的突破并非偶然。林世大回忆,研发团队曾面临三大难关:材料变形机理复杂、模具磨损剧烈、成形精度难以控制。为此,企业构建了“产学研用”协同创新体系,一方面与高校合作建立材料数据库,运用CAE仿真技术模拟冲压过程;另一方面引进五轴联动加工中心等高端设备,将模具制造精度提升至微米级。如今,天津世亚的产品已覆盖30余家主流车企,市场占有率突破25%。
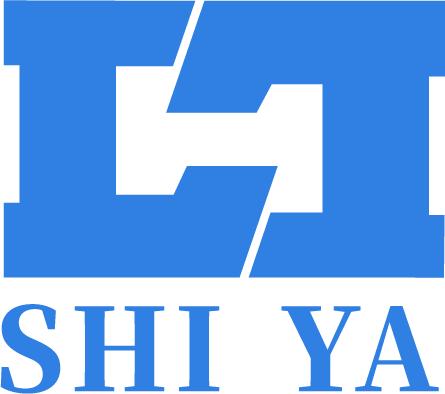
深耕:用标准化体系筑牢品质基石
在天津世亚的生产车间,一块钢板要经过23道工序的淬炼,才能蜕变为合格的模具。林世大强调:“我们建立了从设计、制造到检测的全流程标准化体系。”企业自主研发的模块化设计平台,可将模具开发周期缩短40%,同时通过实施DFM(可制造性设计)规范,使产品一次合格率提升至98.6%。
这种对品质的极致追求,在新能源汽车轻量化浪潮中更显价值。林世大展示了一组对比数据:采用世亚模具生产的超高强度钢车身结构件,比传统热成型工艺减重30%,而抗冲击性能提升25%。目前,企业已为多家新势力车企开发了12款轻量化模具,其中某款电池包框架模具成功实现进口替代,单套模具成本降低60万元。
远谋:以数字化赋能产业升级
面对汽车产业“新四化”趋势,林世大展现出前瞻布局。在天津世亚的智能工厂,AGV小车穿梭于数控机床之间,MES系统实时监控着128台设备的运行状态。“我们正在打造模具行业的‘灯塔工厂’。”林世大透露,通过部署工业互联网平台,企业实现了设计数据与生产设备的互联互通,设备利用率提升至85%,订单交付周期缩短35%。
这种数字化转型不仅体现在制造环节。天津世亚构建了云端模具知识库,集成20余年积累的工艺参数和失效案例,工程师可通过AI辅助设计系统快速调取最优方案。林世大特别提到与大型车企的合作:“我们正在开发基于5G+边缘计算的远程运维平台,未来可实现模具状态的实时监测与预测性维护。”
担当:以民族品牌践行产业报国
作为民营模具企业的代表,林世大对行业痛点有着深刻洞察。他指出,国内模具行业存在“三多三少”现象:中小企业多、低端产能多、同质化竞争多;高端人才少、核心技术少、国际品牌少。为此,天津世亚实施“三步走”战略:第一步,用5年时间完成核心技术国产化替代;第二步,用3年时间建成国家级创新中心;第三步,用2年时间打造全球化服务网络。
在人才培养方面,企业独创“双轨制”成长体系。新入职工程师需在车间轮岗18个月,掌握从熔炼到装配的全流程技能;同时与天津大学共建联合实验室,每年投入营收的5%用于基础研究。目前,企业研发人员占比达32%,拥有发明专利47项,主导制定行业标准3项。
展望:让中国模具闪耀世界舞台
在访谈尾声,林世大描绘了企业发展的“三阶跃迁”蓝图:近期目标(2025年)实现汽车安全件模具市占率超35%,中期目标(2028年)建成智能化无人工厂,远期目标(2035年)跻身全球模具行业前五强。“我们要做汽车模具领域的‘华为’。”他希望,天津世亚也在模具材料、精密加工等领域形成自主可控的技术体系。
当被问及对年轻创业者的建议时,林世大寄语:“模具行业需要‘板凳要坐十年冷’的定力,但更要有‘不破楼兰终不还’的锐气。”他办公室悬挂的“精于工,匠于心,品于行”九字箴言,或许正是天津世亚从地方企业成长为行业标杆的密码所在。
在汽车产业变革的浪潮中,天津世亚模具股份有限公司正以创新为桨,以匠心为帆,驶向智能制造的深蓝海域。这场关于安全与品质的模具革命,不仅重塑着中国汽车工业的基因,更为全球出行安全贡献着中国方案。
【广告】免责声明:本内容为广告,不代表蚌埠新闻网的观点及立场。所涉文、图、音视频等资料之一切权力和法律责任归材料提供方所有和承担。蚌埠新闻网登载此文出于传递更多信息之目的,对此文字、图片等所有信息的真实性不作任何保证或承诺。文章内容仅供参考,不构成投资、消费建议。据此操作,风险自担!!